Сергей Обозов — о внедрении инструментов бережливого производства на АПЗ
27 июня 2019 года, 16:56
Арзамасский приборостроительный завод с рабочим визитом посетил директор по развитию производственной системы ГК «Росатом» Сергей Обозов, который дал оценку работе по внедрению инструментов бережливого производства на предприятии.
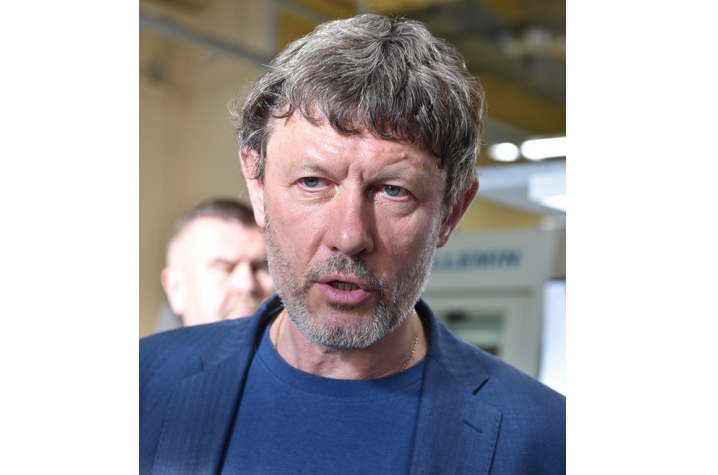
Артем Канашкин, фото: Елена Галкина
Арзамасский приборостроительный завод стал одной из первых площадок по реализации пилотного проекта «Повышение производительности труда и занятости» в рамках программы «Эффективная губерния», инициированной правительством Нижегородской области и ГК «Росатом».
В настоящее время на предприятии идет активная работа по внедрению инструментов Бережливого производства (БП) на основе производственной системы (ПС) «Росатом». Увидеть собственными глазами, как реализуется этот проект, а также ознакомиться с собственными наработками предприятия в области БП было целью приезда Сергея Обозова.
Делегация посетила склад ПКИ центральной складской службы, цеха № 41 и № 53. Представителям госкорпорации показали, как организовано складское хозяйство (процедуры поступления, хранения и выдачи комплектации), сборку изделий и механические участки с ЧПУ, на которых внедрена система автономного обслуживания оборудования (ТРМ).
— Сергей Александрович, ваши впечатления от инструментов бережливого производства, внедренных на площадках АПЗ?
— Мы увидели три проекта, которые сотрудники предприятия сделали самостоятельно на складе комплектующих изделий. Мне очень понравился единый поток. Следующая задача — сокращение запасов на складе. Со своей стороны мы сделали предложение вообще уйти от склада. Так мы поступили в Росатоме, теперь комплектующие идут прямо из производственного цеха в сборочный цех, находящийся в 1,5−2 тысячах км.
— Продукция завода в определенной мере зависит от комплектующих изделий поставщика, их своевременной поставки. Избавившись от склада, нужно вырабатывать максимально точную работу с поставщиком?
— Совершенно верно. Поставщика тоже нужно, так сказать, «воспитывать». Он может грузить вагонами, но может привозить комплект на машине небольшими партиями, ровно столько, сколько нам нужно, в определенное время и прямо в цех. К примеру, десять лет назад на атомных станциях мы организовали подобную работу по поставке воды. Мы заключили договор с поставщиком на весь год, но поставка осуществляется в том объеме, сколько выпито за неделю. Сколько выпили — ровно столько же воды нам и привезли, ровно столько мы и оплатили. Это огромная экономия денег. Нам не нужно, чтобы вода хранилась на складе.
То же самое относится и к комплектующим. Поначалу может возникнуть страх. У любого производства лежит комплект на три-шесть месяцев, так сказать, страховой запас. Но это иллюзия, запасы нужно сокращать. Да, страховой запас должен быть, но ровно в том количестве, которое позволит в случае непредвиденных обстоятельств его использовать. За последние десять лет работы производственной системы в Росатоме мы сократили собственные запасы порядка на 50 млрд рублей по всем видам комплектующих и конечных изделий. Это — живые деньги. При этом у нас еще остались огромные запасы в потоках.
— Откуда вы переняли этот опыт?
— Мы были на предприятиях Японии. Я стоял и смотрел, будто слушал музыку Чайковского: подъезжают огромные фуры, люди разгружают комплектующие, которые на наших глазах тут же уходят на конвейер. А через полчаса-час они уже находятся на машинах, движущихся по конвейеру. Нет вообще никаких складов, даже промежуточных. Ведь можно же так работать.
— Японцы славятся своей точностью и педантичностью. На российском рынке такое возможно?
— Конечно! И нам так сделать можно, мы ничуть не глупее других. А главное, мы не такие богатые, чтобы позволять себе «морозить» деньги, складируя большое число комплектующих. Например, представители Toyota приезжают к нам в гости и говорят: «Вы, русские, богатые люди! Мы себе такого позволить не можем!». Говорят они это, когда видят, сколько на наших складах всего лежит, а сколько изделий уходит в поток. Это вчерашний день. Деньги нужно пускать на развитие, а не на складирование.
— Ваши впечатления от механического производства АПЗ?
— Мы увидели начало хорошей работы по ТРМ — обслуживанию оборудования. Увидели достаточно глубокий производственный контроль на месте. Мы поделились собственным опытом относительно ИСУП (прим. ред.: информационная система управления проектами — программное обеспечение, позволяющее автоматизировать работу персонала, производства, снабжения, складов, логистики и прочее). Мы ее очень аккуратно впускаем в свой производственный процесс. Сначала вручную отрегулировали буквально почасовой и даже поминутный производственный контроль, а уже потом его оцифровали. Машина сама по себе ничего не оптимизирует, необходимо контролировать ее работу.
— Что скажете о сборочном производстве?
— Да, побывали и на сборке. Приятно было увидеть, что много заявок на улучшение дают сами операторы. Были приняты верные решения по компактизации отдельных производств, когда время протекания процесса сократилось на 15%, 25% и даже на 30%, исключены все лишние перемещения.
— Увидели ли вы минусы?
— Я посмотрел на некоторые изделия, сборка которых осуществляется одним оператором от начала до конца. Мне показалось, что можно решиться на применение поточных методов. Мы готовы пригласить ваших специалистов на наш Ковровский механический завод, где статор для газовых центрифуг собираем именно поточным методом. Если вам понравится, вы тоже это внедрите у себя.
— Какой можете подвести итог визиту на предприятие?
— Начало положено хорошее, мы полностью удовлетворены тем, как руководство Арзамасского приборостроительного завода воспринимает методы Бережливого производства. Это значит, что впереди у предприятия много всего интересного.